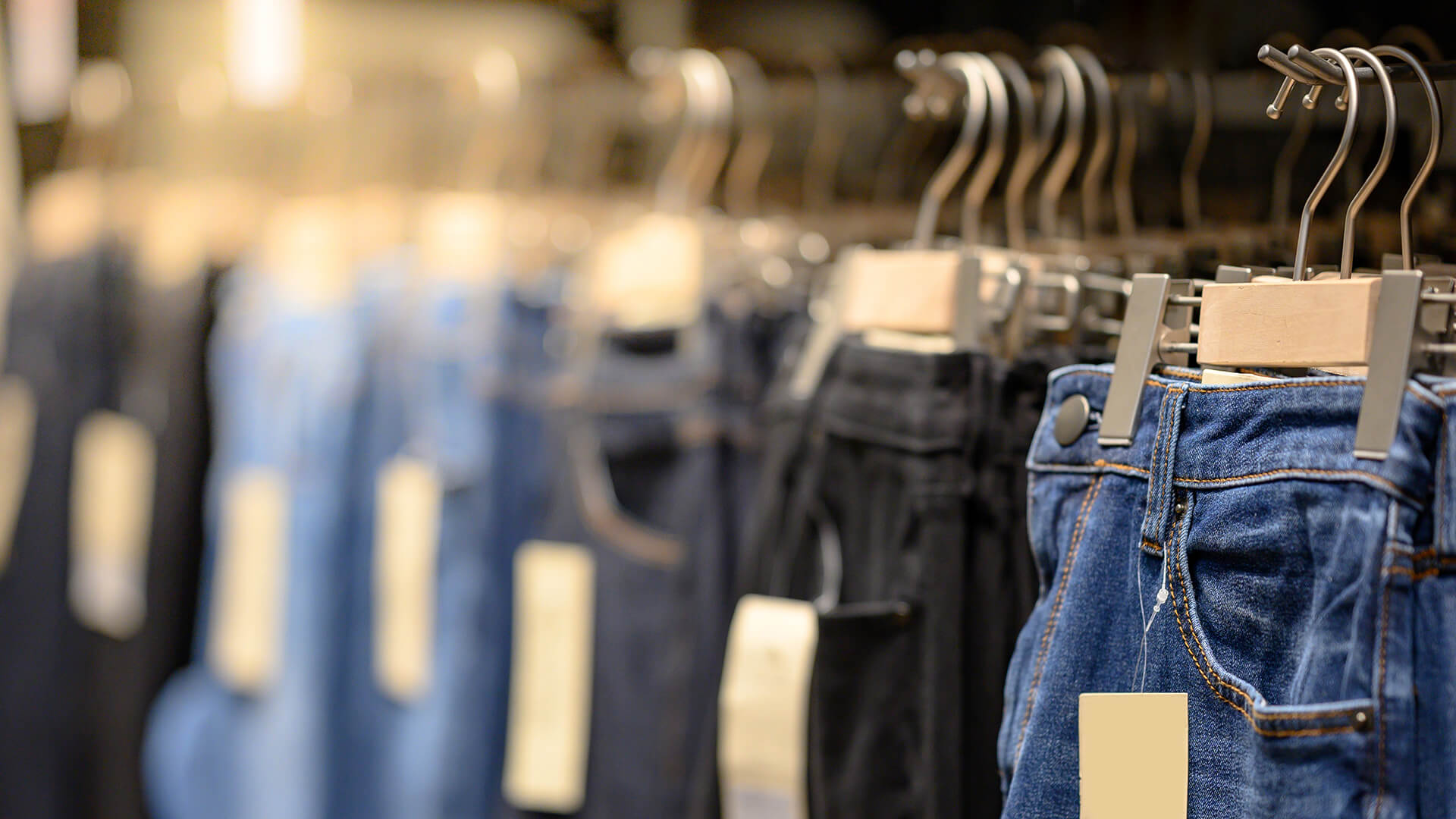
Sample stocktaking for RFIDmanaged fashion inventories
In order to ensure that stocks don’t run out in the warehouse and, above all, in stores, ongoing inventory controls are essential in the interests of transparent and resource-friendly warehouse management. Regular inventory controls are an important element and need to be carried out at least once a year.
Clothes make the man, so the saying goes, which is why fashion boutiques are always well-stocked with suitable and modern fashion items for their customers. But behind the scenes, this requires a fully functional chain of logistical processes. This is because fabrics have to be procured and processed, clothes have to be transported from the production site to the fashion warehouse and stores have to have a steady and sufficient stream of stock. By using sample inventories and intelligent technologies – such as radio frequency identification [RFID] – inventories can be carried out with up to 95% less counting work nowadays. Therefore, sample inventories radically reduce both the financial and the human resources required, they are less prone to errors than the traditional full inventory, and – thanks to their potential uses – are a decisive competitive factor for RFID-managed stocks as well.
Especially for the fashion industry, which is considered to be a global pioneer in the use of RFID technologies along the entire value creation chain, sample inventories form an efficient foundation for well-sorted clothes warehouses. Both industry and logistics have long recognised the potential of RFID technologies, which can be used for contactless identification goods over a wireless signal and without any need for visual contact through the use of an RFID reader. And even in trade, RFID is becoming more widespread for merchandise coding purposes. In the clothing trade, RFID has been helping to take customers’ heightened service and product availability demands into account. The wide variety of products in fashion companies – due to the availability of individual items in different sizes and colours, for example – goes hand in hand with a huge amount of picking work.
RFID records products automatically and drastically cuts costs, which gives in-store employees more freedom to meet customer requirements. Therefore, the fashion industry is considered a pioneering sector with respect to the use of RFID technologies. Goods identification over radio waves helps to avoid shipping errors, incoming goods pallets can be checked more quickly and readout devices used in-store prevent undetected shoplifting among other things. But that’s not all. The technology also makes things easier for the inventory, which takes place at least once per year, and regular inventory controls, provided that these processes are performed in a time-saving manner by means of random samples.