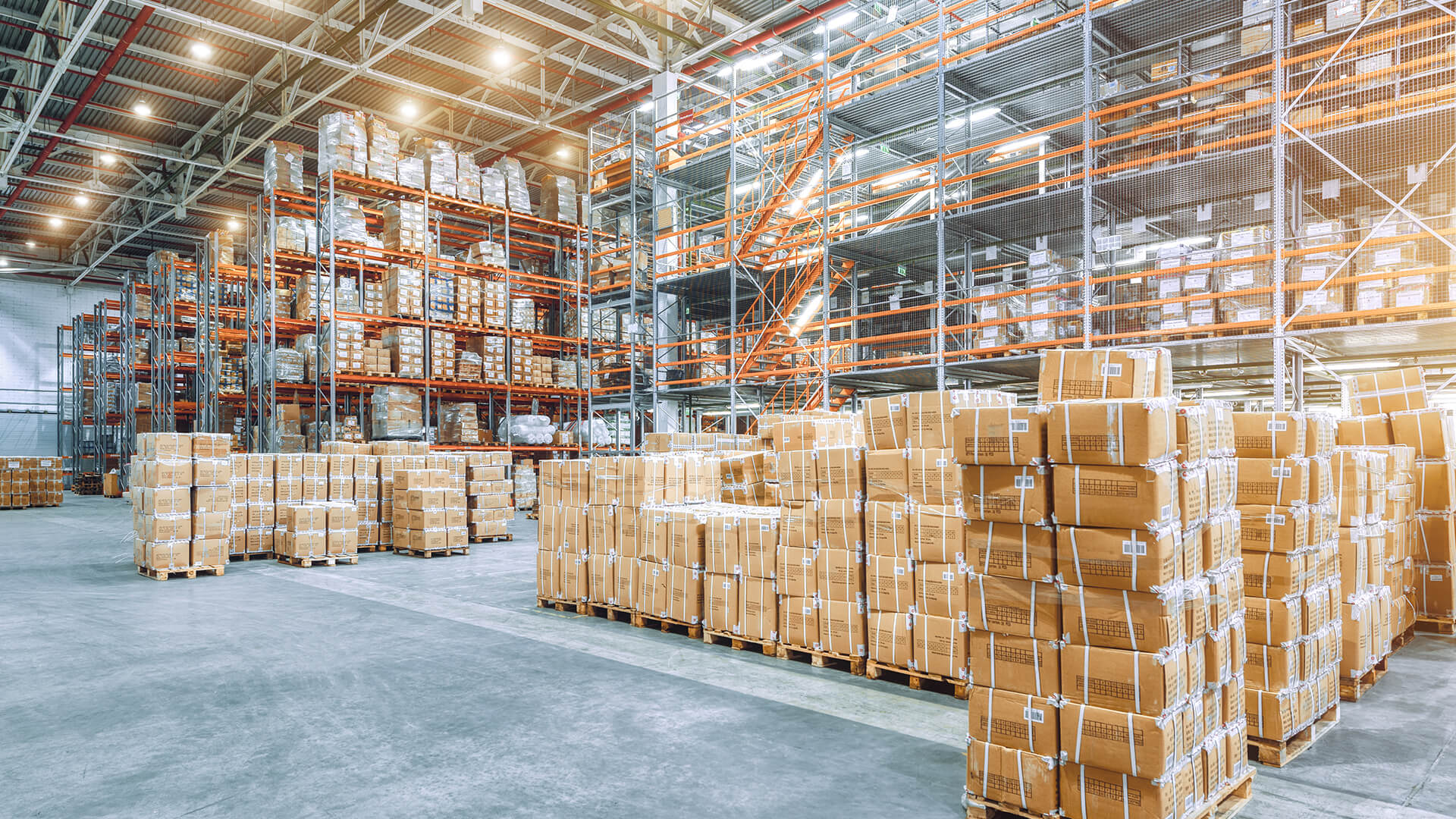
Inventory management: 6 reasons why an ERP solution is not enough
Do I really need special inventory management software if I already have an ERP system in use? Many purchasing and supply chain managers still mistakenly believe that an ERP system and Excel are enough – saving on the wrong end. The question of the need for inventory management software is quite simple to answer: Do you value efficient and modern scheduling? If the answer is yes, it is important to rely on intelligent inventory management software. We explain this in our blog post.