Backshop Tiefkühl GmbH Chooses Replenishment with REMIRA LOGOMATE
Best-before dates, seasonalities and demand determination: The challenges in the food industry are high. To master them successfully, Backshop Tiefkühl GmbH has been relying on REMIRA LOGOMATE since the middle of 2022. The inventory management software enables the company to determine and forecast the demand for all articles in order to avoid out-of-stock situations as well as to reduce the replenishment effort through automated processes.
Maik Sträuber, Head of IT/Purchasing NHW at Backshop Tiefkühl GmbH, was looking for new software and came across REMIRA during his research. "In the previous software, bills of materials as well as pack and label items were not linked to each other, which led to additional work, errors and poorer determination of requirements. It was important to us for the future that we achieve a demand-based determination for bills of materials, packing and label articles with different storage times and sales units. With LOGOMATE, we can meet exactly these requirements." The fact that the software is also already being used by numerous large and small retail companies was another crucial point in the decision-making process, according to Sträuber.
From Manual to Automated Disposition
The inventory management software also convinced those responsible at Backshop with its improved analysis and forecasting functions and improved transparency for sales items with different order item numbers.
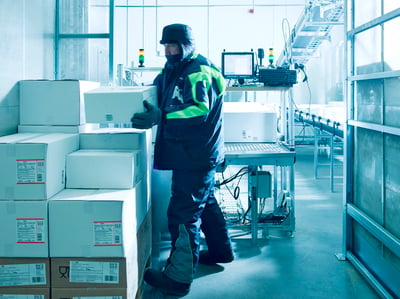
As a subsidiary of Harry Brot GmbH, the company has an extensive and high-quality range of frozen bakery products and supplies both the bulk consumer and LEH sectors as well as B2B. In addition to a management-by-exception function and automated ABC/XYZ analyses, LOGOMATE also provides automatic disposition suggestions and orders. Especially the latter was a decisive criterion for Maik Sträuber:
"We wanted to reduce our replenishment effort through automations. Previously, highly manual processes had made vacation and sick leave replacement enormously difficult for us - scheduling can now be made much easier for the entire team with the help of the software solution."
Backshop has also seen other benefits in recent months: Problems with best-before dates and impending out-of-stock situations can be identified more quickly and rectified before they occur. In addition, the planning of seasonal items, such as Berliners, is easier and more precise thanks to REMIRA's inventory management solution.
VMI as an Option for the Future
LOGOMATE also enables the implementation of Vendor Managed Inventory (VMI), which could be of further interest to Backshop in the future. For this, Backshop could easily dock the software to the ERP systems of the respective retailers using standard interfaces.
"For interested partners, we could imagine implementing VMI to avoid a bullwhip effect. The resulting increased transparency and even better coordination between the players would benefit our customers and ourselves equally, for example from an improved flow of goods and fewer out-of-stock situations."
Another special feature of the project at Backshop was that the company not only works with the basic unit "piece", which is relevant for production, but also with cartons in materials planning. For this reason, the REMIRA team further developed the display in certain units. Thus, Backshop can now display the BBD in the desired unit via mouse-over. Another advantage was that IT is located directly on site in the company building. This meant that communication channels were short during the introduction and implementation of the software. Maik Sträuber was also more than satisfied with the colleagues from REMIRA:
"With the professional and technically competent sales team, the cooperation was a lot of fun from the very first minute, and the project team was also optimally staffed both professionally and personally. The entire project work as well as the handover to support went smoothly."
Related Link
Photos: © Backshop